In an HDD, the task of positioning the read-write head falls to the hard drive actuator assembly, which moves the actuator arm to which the head is attached. Positioning and holding the read/write head accurately isn’t easy when billions of bits are spread over platters revolving at thousands of times per minute. The fact that all this takes place in a confined space with hundreds of other component parts makes actuator design all the more tricky.
Meeting these challenges and ensuring that an actuator performs well over an HDD’s whole life-cycle requires careful design. Ultra-high precision and speed are key to overall HDD performance, and malfunctions can result in corrupted or lost data.
Actuator technology has evolved significantly over time, and will continue to do so. New approaches include triple-stage actuators, and the inclusion of more than one actuator within a single HDD. These innovations enhance the speed, accuracy and reliability of the actuator assembly to meet demands of higher storage and quicker access.
Inside the Hard Drive Actuator
In mechanics, “actuator” is a general term for any device which converts energy into motion. In this case, the hard drive actuator moves the actuator arm, aligning the read/write head on the HDD platter with exceptional accuracy and speed. This impacts drive performance, since quicker alignment means smoother read/write operations.
The assembly is governed by the HDD controller, which you can think of as the center of communication between the computer, the actuator, and the read-write head. It guides the actuator arm by translating signals between the CPU and the actuator through a subsystem called the voice-coil controller. Beyond that, the HDD controller synchronizes the platters and the actuator, manages data transfer, and handles error correction.
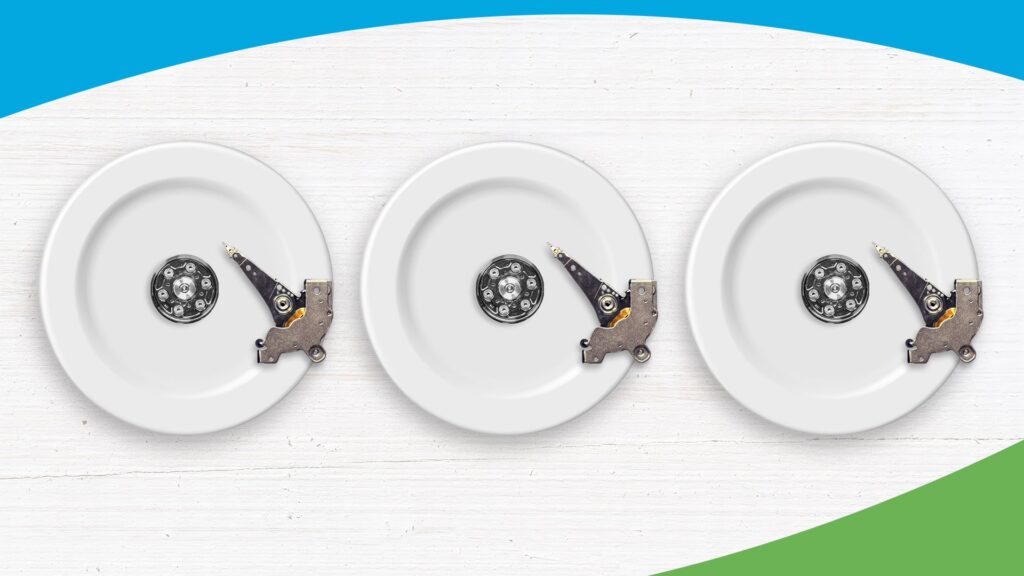
Related Reading
Actuators effect performance, but when it comes to density, plates are paramount. Platter design plays a key role in enabling high-cap storage and reducing cost-per-TB.
What Goes Into Hard Drive Actuator Design?
Stepper Motors
In the early days of the technology, HDDs used stepper motors as part of the actuator assembly. These motors moved the hard drive actuator arm to the desired location by converting digital signals into mechanical displacement.
While initially workable, it became inadequate as the areal density of HDD platters increased, since narrower tracks and closely packed magnetic bits require more accuracy than stepper motors allow. Another issue was that stepper motors generate heat, which could cause platters to expand just enough to risk a head crash—when the read/write head comes into physical contact with the HDD platters.
Voice Coil Motors
To overcome these limitations, the industry moved to the now standard voice-coil motors, which are integrated into the actuator assembly using a servomechanism. A servomechanism is a feedback loop that continuously monitors and adjusts the actuator arm based on real-time inputs, ensuring that the read/write head remains in perfect alignment. The transition to voice-coil motors led to a significant improvement in HDD performance, and enabled higher storage capacities by allowing the use of complex data structures on the HDD platters.
Reliability
Like all mechanical parts, actuators have limitations and are vulnerable to failure. Over time, they can become misaligned or just fail to work. This could be due to several factors, such as wear and tear of components, gradual misalignment, or the malfunction or any one of the interconnected parts. When the actuator malfunctions, the consequences can be severe for the integrity of the HDD. Users might hear strange noises from the HDD, experience data corruption, or even suffer permanent data loss due to a head crash.
These challenges underscore the need for a reliable actuator design. To meet these challenges, HDD manufacturers like Seagate, Western Digital and Toshiba design and manufacture their actuators in-house apart from a few specialized components. Technological innovations in actuator design like Seagate’s multi-actuators or WD’s triple-stage actuators gives them a competitive edge in a market that constantly demands higher capacity and speed.
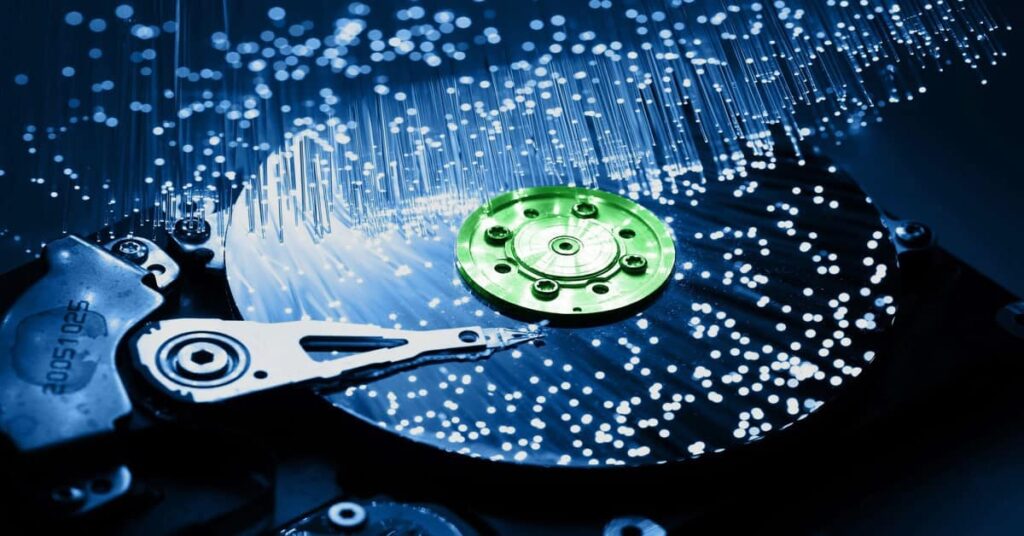
Related Reading
While the actuator moves the read/write arm, the spindle is what puts the spin in disk media. Achieving high rotation speeds in a compact space is key to overall drive performance.
More Actuators for a Faster Future
While HDDs are preferred for reasons of cost, rather than speed, throughput still matters. This is especially true for hyper-scale data centers and commercial enterprises that must maintain high levels of performance without compromising capacity. To address these performance requirements, some manufacturers have introduced multi-actuator technology. As the name suggests, these incorporate more than one actuator into a single drive.
A leading example is Seagate’s MACH2 drives, which employ two independent actuators operating simultaneously. This setup creates a parallel system of two concurrent channels for data input and output. It effectively doubles the IOPS (input/output operations per second) rate by allowing data access from two sections of the drive at the same time.
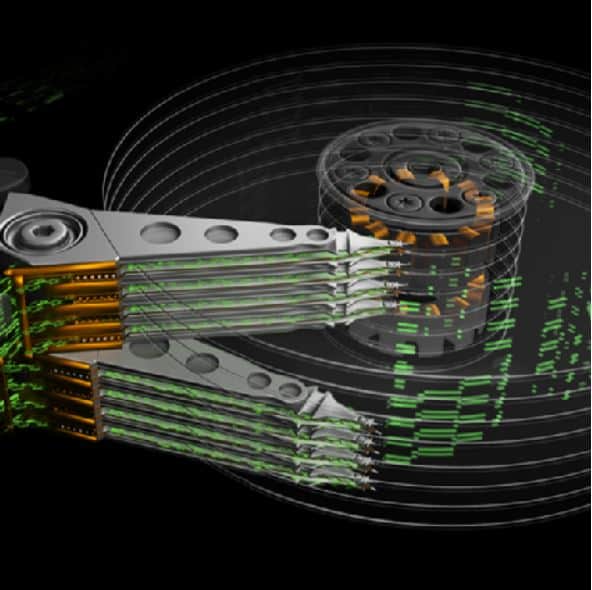
Compared to single-actuator drives, Seagate reports high performance gains in parameters such as random reads, high transfer size (128KB+) random writes and sequential reads/writes. These performance parameters make dual-actuator drives ideal for demanding applications like content delivery networks, video streaming and cloud applications. Beyond speed, this technology also enhances the relative power efficiency of the drives.
Western Digital is also advancing in this area with its Ultrastar DC HS760 drive. This drive makes use of dual-actuators to address challenges of rapid data access and consistent performance in high-capacity drives. Ravi Pendekanti, WD’s SVP of HDD product management, has an amusing analogy: “Imagine you’re using one hand to try to find a single pair of socks…It might be quick in a small bin, but it gets harder in a five-gallon laundry basket, or a 25-gallon basket, and so on. As the size of the container gets bigger, things get so much easier when you can use both hands.”
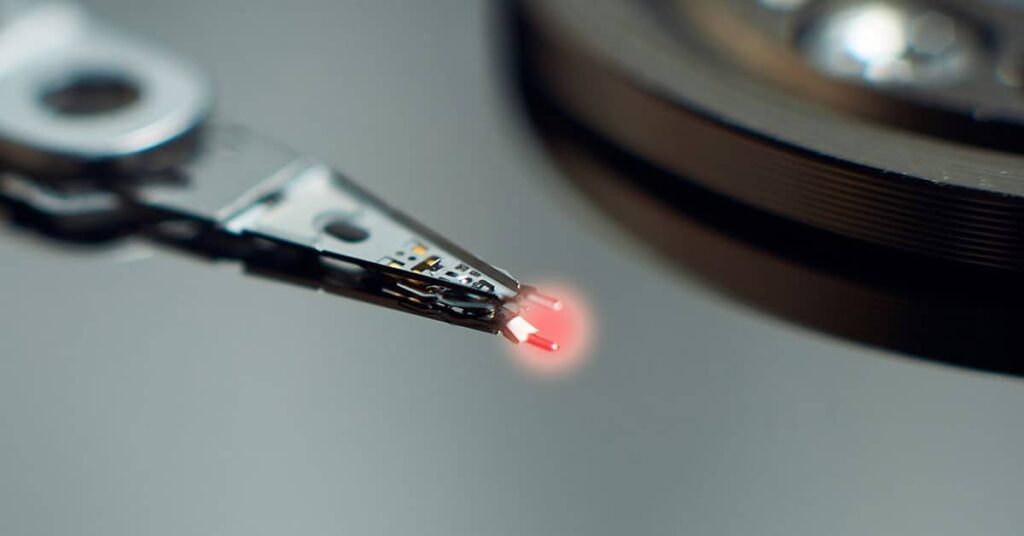
Related Reading
HAMR drives, which use lasers to temporarily lower the magnetic coercivity of grains during the write process, are at the forefront of efforts to increase areal density.
Multi-Stage Actuators
Rising areal density in storage media means that the space between the stored bits keeps shrinking, requiring extraordinary precision by the actuator in positioning the read/write head.
For example, in a 2.5 inch HDD, the components are packed tight with such a slim margin of error that sound vibration from built-in laptop speakers can cause head misalignment. Furthermore, the actuator arm moves over the platters’ concentric tracks in an arc, creating alignment challenges between the tracks and the read/write head. This is particularly true when the head moves towards the inner and outer edges of the circular platters.
To overcome these complications, modern HDDs employ multi-stage actuators (not to be confused with multi-actuators) by integrating supplementary actuators in the actuator arm along with the voice-coil motor. Think of these as extra “joints” in the actuator arm. The additional actuators enable ultra-precise control of the read/write head positioning.
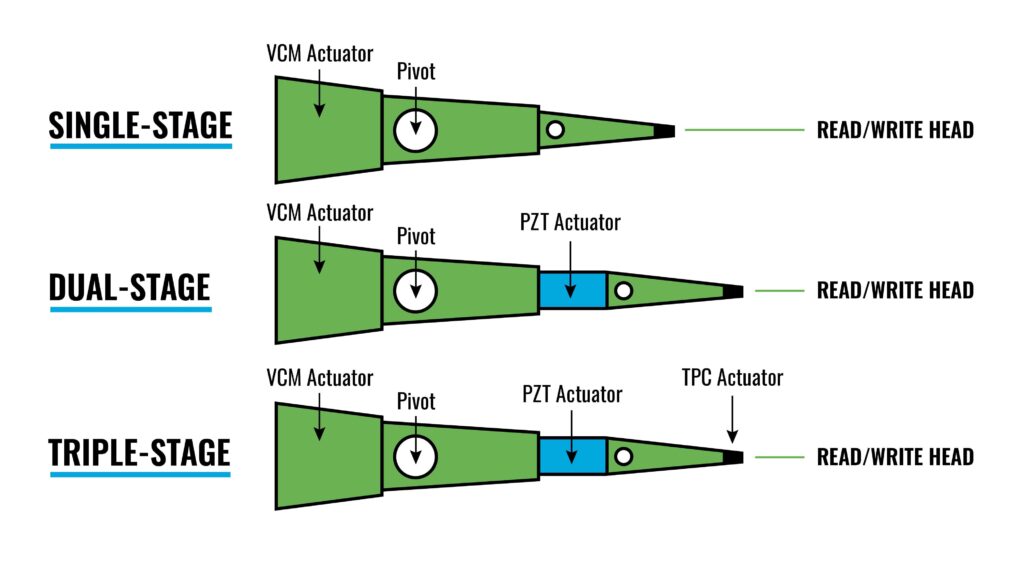
Western Digital’s dual-stage and triple-stage actuator technologies illustrate this advancement. A dual-stage actuator initially incorporated a milli-actuator as a secondary pivot point, allowing adjustments as fine as 200 nm. Later on, an upgraded dual-stage actuator replaced a milli-actuator with a micro-actuator, which is capable of adjustments of 100 nm. “If you think of it like driving on a curving, multilane highway, the first-stage actuator puts you on the highway, and the second, fine-tuning stage keeps you centered in the correct traffic lane” explains WD in its whitepaper.
Eventually, triple-stage actuators combined both milli-actuators and micro-actuators to provide three pivot points in a single-actuator assembly. These supplementary actuators rely on piezoelectric (PZT) elements to execute micro-adjustments. The piezo elements expand and contract enabling minute repositioning of the read/write head once the voice-coil motor positions the actuator arm. Additional actuators also mitigate internal and external vibrations, making sure the head remains in position.
In addition to improving read/write head positioning accuracy, multi-actuators enhance HDD performance. Faster and precise head movements boost overall speed of the drive, which is essential in managing high-density data. The pin-point accuracy of a multi-stage actuator also lets manufacturers pack together data tracks and bits without increasing error rates.
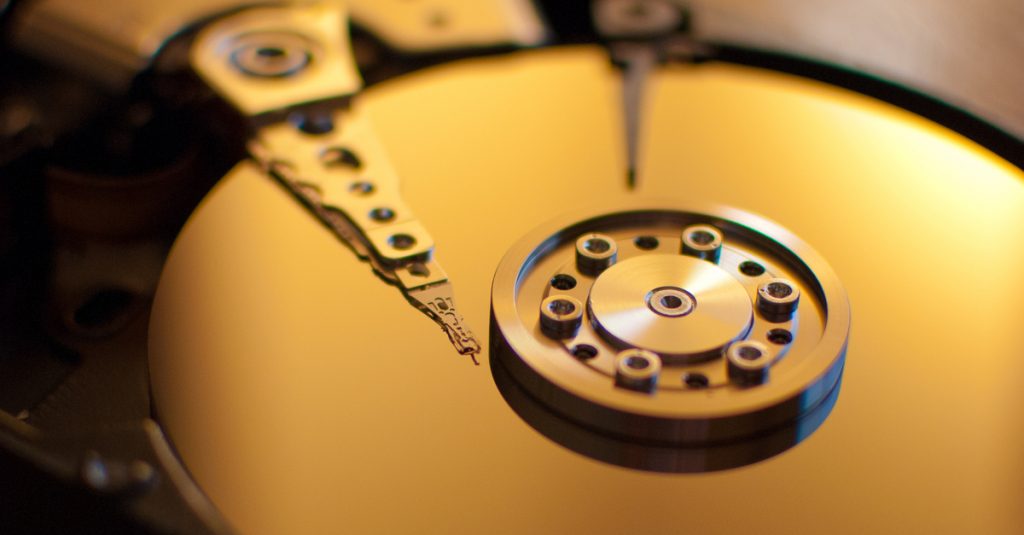
Related Reading
While flash is a natural fit for low-latency operations, the role of HDD in nearline storage at scale is secured, at least for now, by its lower cost-per-TB.
A Call to Arms
Hard drive actuators have come a long way from the days of simple stepper motors. As storage densities increased, voice-coil motors changed the game, addressing the need for better precision and heat management. Today, the demand for greater capacity and performance is pushing companies to innovate further by developing dual-actuators and multi-stage actuators.
Advancement in actuator technology has a wide ranging effect on the HDDs. It not only enhances speed but also pushes the frontiers of higher storage capacities. At the same time, it makes HDDs reliable by safeguarding data integrity, which is critical for both consumer and commercial applications. This ensures HDD remains competitive in an evolving data landscape, and actuators continue to play a key role in keeping HDDs relevant.
At Horizon Technology, we know all about data center HDD. For practical support with procuring drives, get in touch and find out how we can help.